
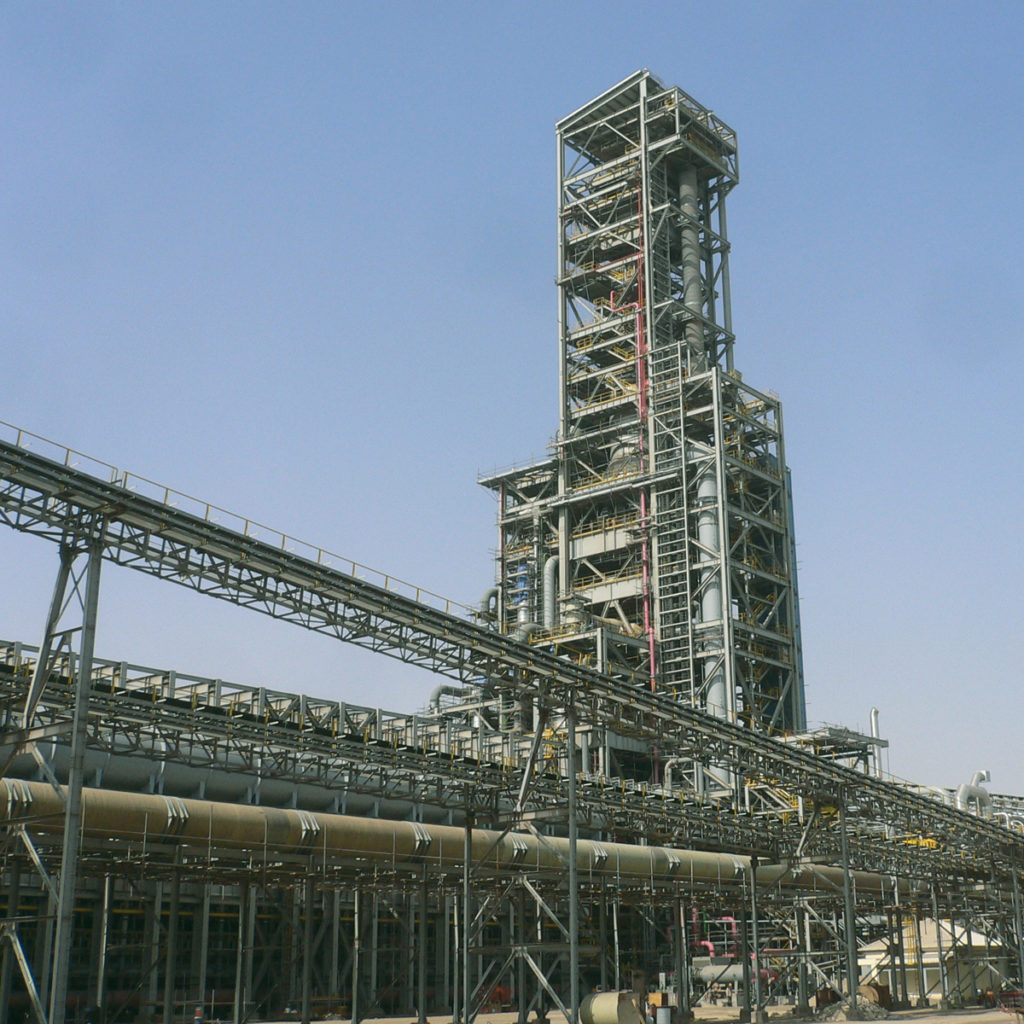
Midrex shaft furnaces with 5.0 m, 5.5 m, and 6.5 m shaft diameters having annual production capacities of 800,000 tons, 1 million tons and 1.6 million tons of DRI respectively constitutes different development stages. The maximum production capacity of a Midrex unit in 1984 was 600,000 tons per year. These were all integrated in the early 1980s, making the process nearly complete. On the other hand, Midrex Technologies also carried out various improvements to the plants they built in various countries. Kobe Steel significantly modified the design, exploiting the company’s technologies developed through blast furnace operation, and stabilized the then new process. The process was immature in 1978, when Kobe Steel began the construction of a plant with a production capacity of 400,000 tons/year in the State of Qatar. Each year since 1987, DRI production through Midrex process is over 60 % of the total global production of DRI. Production from many of the Midrex plants exceeds their design capacity. Since 1969, DRI production through Midrex process has crossed 500 million tons. Donald Beggs’ concept of combining stoichiometric natural gas reforming with shaft furnace direct reduction of iron ore was a breakthrough innovation which has stood the test of time. The genius of the Midrex process is its simplicity. The first commercial plant, having a production capacity of 150,000 tons per year, was built in Portland, Oregon, in 1969. A pilot plant was built in Toledo, Ohio in 1967. It is now a wholly owned subsidiary of Kobe Steel. The original process was developed by the Midland-Ross Co., which later became Midrex Technologies, Inc. The history of the Midrex process goes back to 1966 when Donald Beggs of the Surface Combustion Corporation conceives the idea for the Midrex direct reduction process. The principle of the reduction process using reducing gas is shown in Fig 1.įig 1 Principle of reduction process using reducing gas
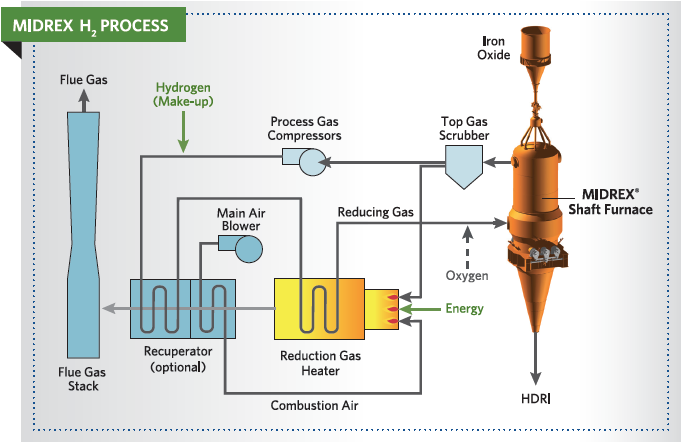
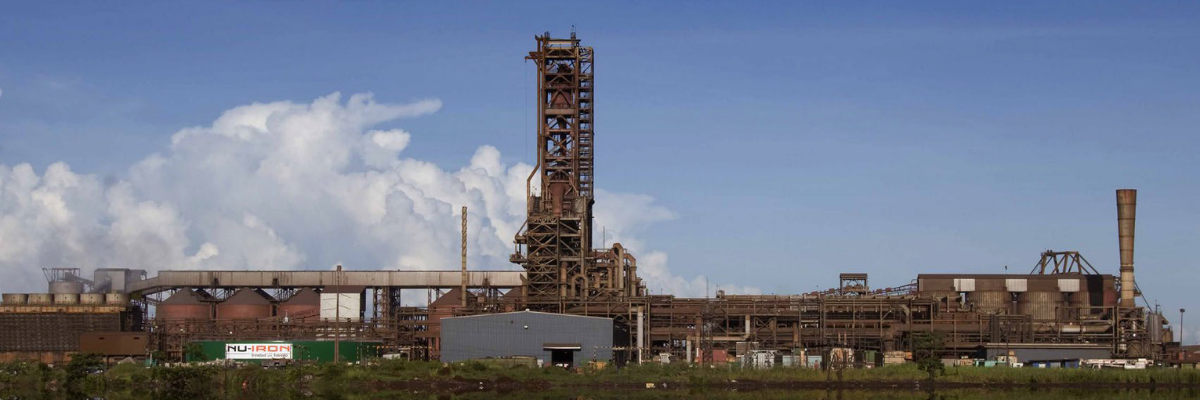
It is a gas-based shaft furnace process is a solid state reduction process which reduces iron ore pellets or lump ore into DRI without their melting using reducing gas generally formed from natural gas. Midrex is an ironmaking process, developed for the production of direct reduced iron (DRI). C reduction, carburizing, CDRI, DRI, H2 reduction, HBI, HDRI, Hot link, Midrex process, Reformer, Shaft furnace ,.In recent years, Kobe Steel together with Midrex have developed our own new process, the "FASTMET ® Process" taking a step forward into a new field of Direct Reduction.Midrex Process for Direct Reduction of Iron Ore We take pride in the fact that our plants are able to perform at or above capacity with smooth and stable operations. Of several Direct Reduction processes producting DRI, the MIDREX ® DR Process, which was developed and is owned by Midrex Technologies,Inc., a wholly-owned subsidiary of Kobe Steel, accounts for about 60% of world wide prodution.Īs a licensee of the MIDREX ® DR Process, Kobe Steel has supplied many MIDREX ™ DR Plants all over the world. Recently, while the production of steel via the Blast Furnace route are increasing only slightly, production via the Direct Reduction Plant route have dramatically increased.
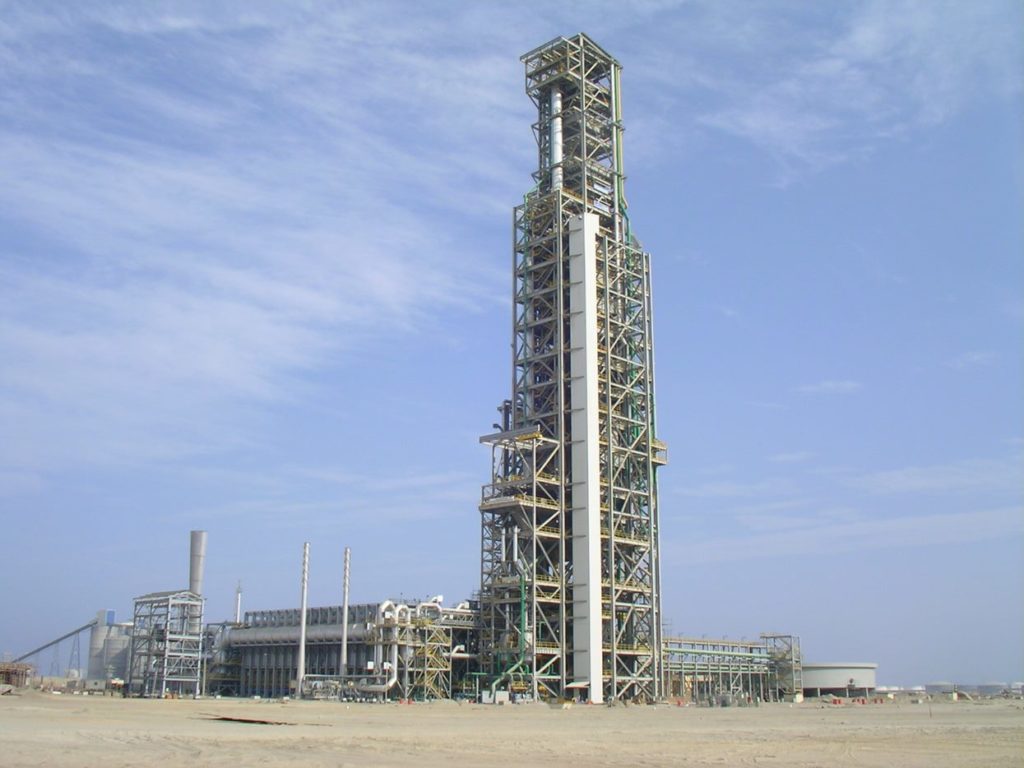
Recently, however, even in developed countries, such as the United States, Direct Reduction Plants are drawing more and more attention as a way to provide a stable supply source of pure iron, substituting steel scrap. As Direct Reduction Plants are not built on the same, enormous scale as Blast Furnaces, their investment costs are lower, and they have been mainly constructed in developing countries where natural gas is relatively inexpensive. Direct Reduction is an iron making process for the new era, which utilizes natural gas to reduce iron ore to produce Direct Reduced Iron (DRI).
